Está buscando implementar o lean thinking em sua empresa sem dominar e aplicar o MFV (mapa de fluxo de valor)?
Pois saiba que o MFV é considerado uma das ferramentas mais importantes para o sucesso em uma jornada lean!
Um mapa de fluxo de valor (value stream mapping – VSM) bem feito é um dos alicerces da implementação assertiva do pensamento enxuto em uma organização. Isso porque ele ilustra de forma simples a aplicação ou não dos princípios que a Toyota tanto prega. O VSM traz um jeito fácil para que aprendamos a enxergar os nossos processos de uma maneira metódica, mostrando com clareza qual caminho seguir em nossa jornada lean.
Entendeu ou quer que eu desenhe? (Um MFV, é claro!)
Antes de iniciar, prepare os materiais necessários:
- Prancheta com folhas de rascunho para os desenhos;
- Lápis e borracha (é comum modificarmos o desenho ao longo do desenvolvimento);
- Cronômetro para fazer medições.
- EPI’s necessários para visitar os processos.
Dicas do consultor:
- Um MFV deve ser confeccionado caminhando pelos processos e fazendo as medições no momento da confecção;
- Ao chegar em cada processo a ser mapeado, converse com a liderança e explique aos colaboradores que a atividade está sendo feita para buscar oportunidades de melhoria, não para julgar ou criticar negativamente o trabalho de alguém. Peça para que TODOS os problemas sejam mostrados.
- O fluxo de valor deve ter um responsável, que montará a equipe, conduzirá as atividades e acompanhará ações e resultados;
- Não espere o mapa perfeito (ou bonito) para começar a implementação
ele nunca será perfeito, adapte durante a implementação; - Não desista, o que parece impossível pode ser alcançado ao longo prazo.
Então vamos ao que interessa: Aprender a criar um BOM mapa de fluxo de valor!
Para aplicar a ferramenta corretamente e ter sucesso na aplicação do pensamento enxuto, precisamos seguir 4 passos simples:
- Definir uma família de produtos: Desta forma, teremos o foco em uma única linha produtiva, composta por produtos que passam pelos mesmos processos para serem produzidos.
- Desenhar o Mapa do Estado Atual: Aplicar a ferramenta de forma prática, utilizando os símbolos padrão e coletando dados reais no local de trabalho no momento da aplicação.
- Desenhar o Mapa do Estado Futuro: Analisar o mapa atual e, seguindo os conceitos do lean thinking, desenhar um mapa ideal de como o fluxo deverá funcionar após um período de tempo predefinido (3 meses, 1 ano, 5 anos…).
- Criar um Plano de Implementação: Definir as melhorias necessárias para transformar o estado atual no futuro, dividi-las em ações com datas de realização possíveis e delegar cada ação a um responsável com condições e autonomia para realizá-la.
Passo 1. Definir a família de produtos
Organize uma tabela onde cada coluna represente um processo produtivo e cada linha represente um produto. Em seguida, analise o primeiro produto marcando um X em cada processo no qual este produto sofra alguma transformação. Após analisar todas as linhas, separe os produtos que passam pelos mesmos processos produtivos e nomeie como uma família (conforme ilustração abaixo).

Antes de passar ao passo 2, vamos definir o nível de abrangência do nosso estudo:
- Nível do processo – Quando o VSM é feito para estudar um único processo dentro de uma organização. Geralmente ele é aplicado por líderes, encarregados ou gerentes de uma linha de produção.
- Nível da planta – Quando os mapas atual e futuro são desenhados contendo dois ou mais processos que vão da entrada da matéria prima até o produto acabado dentro de uma mesma planta.
- Múltiplas plantas – Quando aplica-se o MFV em duas ou mais plantas produtivas filiais.
- Múltiplas empresas – Quando mapeiam-se os fluxos de toda uma cadeia produtiva, iniciando-se em uma organização que fabrica insumos, passando pelas fábricas de transformação, empresas de distribuição e varejo, chegando no cliente final.
Independente do nível escolhido, a ideia é a mesma: Otimizar o fluxo de atividades para entregar maior valor em um menor espaço de tempo e sem desperdícios até o processo subsequente.
Passo 2. Desenhar o Mapa do Estado Atual
Tanto o MFV atual quanto o futuro possuem 3 componentes essenciais:
- Fluxo de informações
- Fluxo de Materiais
- Linha do tempo
No exemplo abaixo podemos conferir cada um destes componentes essenciais, assim como um caminho ideal para confecção do mapa, iniciando no canto superior direito com o símbolo do “cliente” e percorrendo os fluxos de informação e materiais conforme mostram as setas amarelas no sentido anti-horário. Em seguida, colocam-se os dados de programação seguidos pela linha do tempo. Esta é a forma mais comum de confeccionar o mapa, embora alguns especialistas lean prefiram fazer o sentido horário à partir do cliente (caminho inverso).
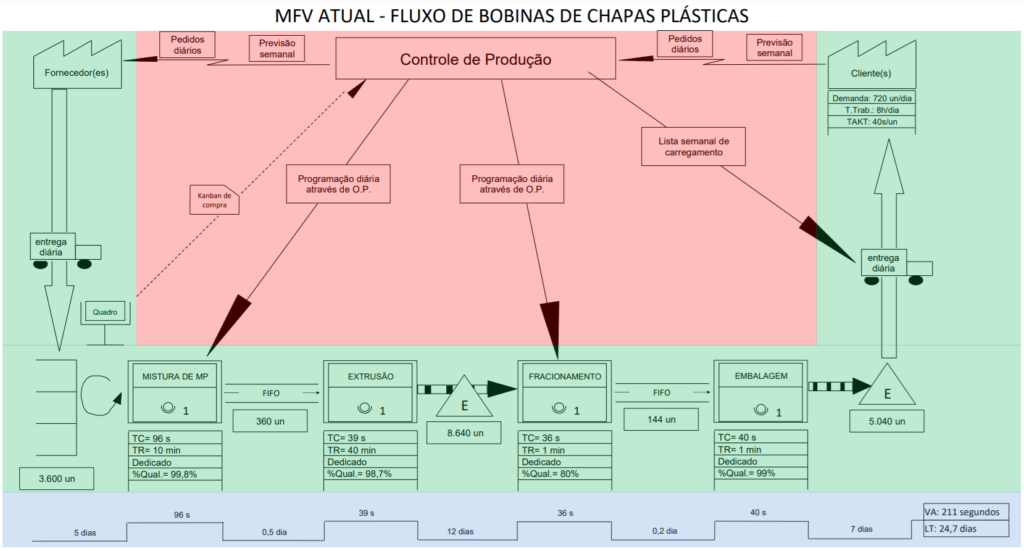
Logo abaixo, temos uma lista com os símbolos mais comuns utilizados na confecção do MFV atual e futuro, mas você pode adaptar estes símbolos ao seu próprio gosto, desde que as informações fiquem claras à você e à toda a equipe.
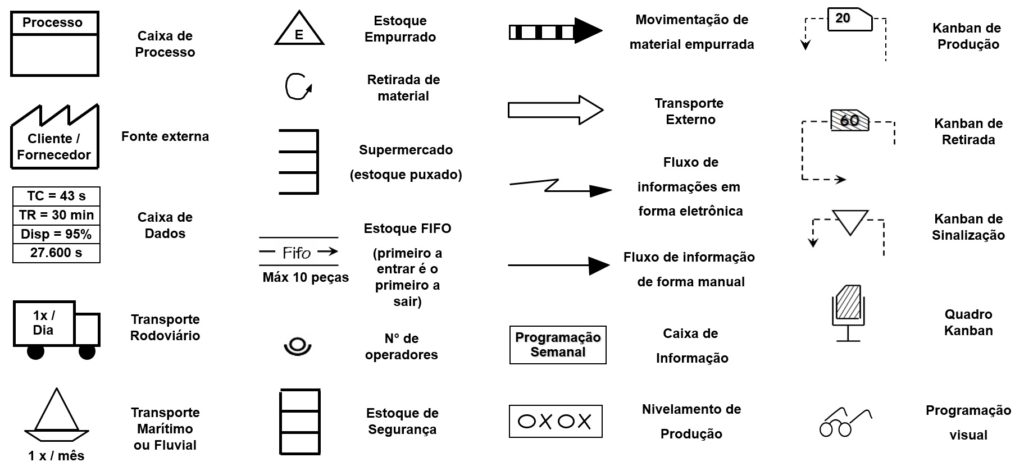
Na caixa de dados do cliente, colocamos informações que nos indicam o ritmo da produção: A demanda e o Tempo disponível.
O TAKT é o melhor indicador para isso, pois ao dividirmos o Tempo disponível / Demanda, temos como resultado o valor de tempo de ciclo que cada processo terá que superar para que a fábrica como um todo atinja a produtividade ideal.
Nas caixas de dados dos processos, geralmente colocamos os seguintes dados:
- T/C (tempo do ciclo / cycle time): Quantos segundos o processo demora para fazer uma unidade do produto (segundos por metro, por exemplo);
- TR (tempo de troca / change over time): Tempo de setup, desde a última peça boa do produto “A” até a primeira peça boa do produto “B”;
- Disponibilidade (disponibilidade real da máquina) – Percentual em que a máquina está funcionando comparando com o tempo que ela estava programada para funcionar;
- % de Qualidade – percentual de produtos bons em função do total produzido;
- Dedicado/Compartilhado – Se o processo produz apenas para este o fluxo (dedicado) ou para outro fluxo também (compartilhado);
- Número de Operadores que trabalham neste processo;
- Número de Variações do Produto;
- Tamanho da Embalagem;
- Tempo de Trabalho (descontando os intervalos);
- Qualquer outro indicador importante para avaliar o bom funcionamento do processo.
Passo 3. Mapa do Estado Futuro
Seguindo a mesma lógica e símbolos utilizados no passo anterior, esta é a hora de refletirmos sobre como tornar o nosso fluxo o mais enxuto possível dentro de um prazo predefinido – 6 meses é um ótimo prazo. O mapa futuro deve ser criado olhando para as necessidades do nosso cliente e para os objetivos do nosso negócio.
Criando um fluxo de valor enxuto:
- Procure os 8 desperdícios no mapa atual e faça mudanças para eliminá-los ou reduzi-los no mapa futuro;
- Equilibre o processo produtivo – a eficiência geral é mais importante do que a eficiência do processo;
- Produza em cada processo de acordo com o TAKT (falamos sobre ele no passo 2);
- Desenvolva fluxo contínuo (sem paradas, distâncias ou estoques) onde possível, e crie supermercado puxado onde o fluxo contínuo não é possível/viável;
- Busque programar apenas um processo e fazer com que ele dite o ritmo dos demais (produzindo somente quando e o que for necessário)
Segue abaixo um exemplo de mapa futuro:
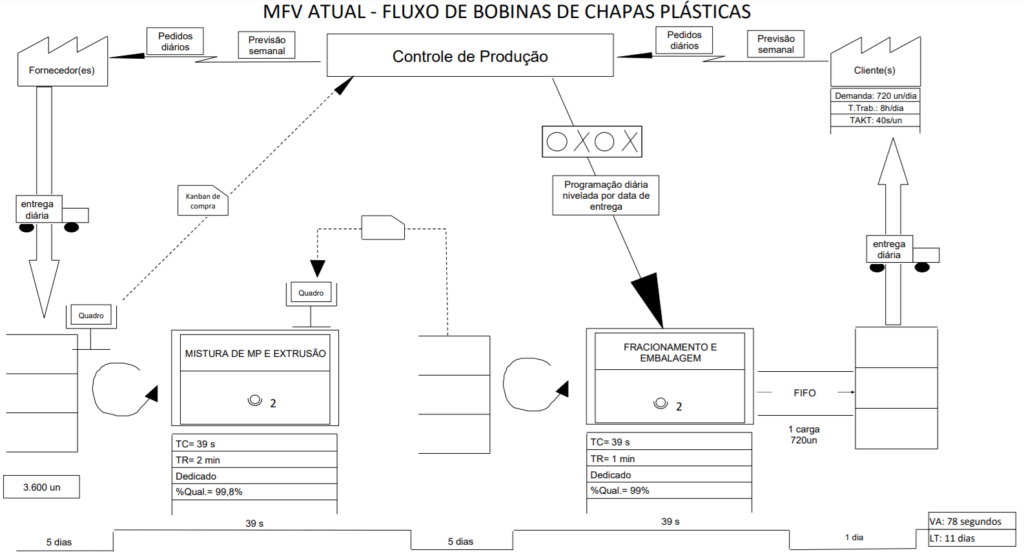
Lembrando que este é apenas um exemplo, e que as modificações feitas neste mapa são meramente didáticas, você precisa olhar para o SEU fluxo e pensar naquilo que é melhor para a SUA empresa!
Passo 4. Plano de implementação
Para sairmos do estado atual e chegarmos ao futuro no prazo predefinido, devemos dividir o nosso plano de implementação em loops (grandes etapas) e reduzir estas etapas em kaizens ou ações de melhorias executáveis.
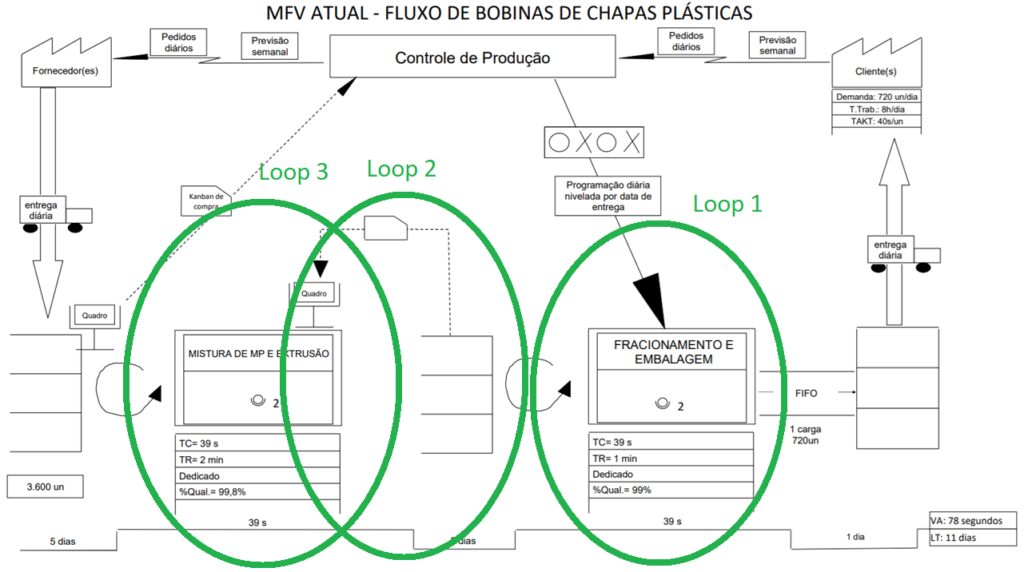
Em seguida, traçamos um plano de ação no formato 5W2H, Gantt ou outra ferramenta de sua preferência (pode ser o plano de ação padrão da sua empresa). Deixe um prazo atingível para cada ação, definido junto a cada responsável e cobre o atendimento de forma justa – afinal o responsável escolheu seu próprio prazo.
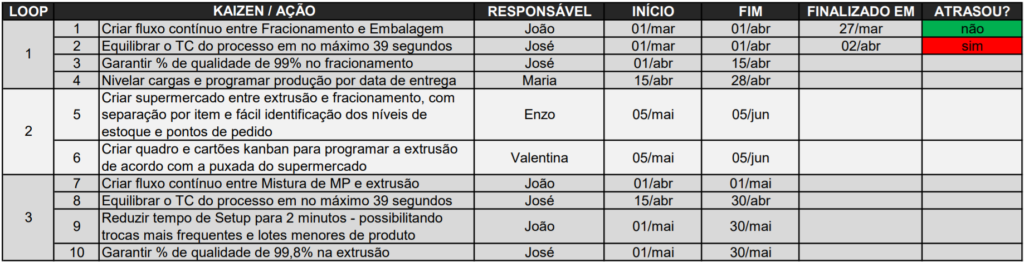
Por fim, a equipe deve definir uma forma de avaliar o cumprimento e a eficiência de cada ação. Isto pode ser feito através de reuniões com frequência definida com visitas aos processos. Cabe ao responsável pelo fluxo de valor conduzir os trabalhos com disciplina e garantir as melhores condições de trabalho à toda equipe.
Lembrando que o MFV, assim como a maior parte das ferramentas do lean thinking pode ser aplicada em qualquer tipo de negócio. Afinal, todas as organizações existem para entregar VALOR a algum público, certo?
Gostou do artigo? Deixe um comentário para ajudar a comunidade a crescer!
Caso tenha dúvidas ou queira conhecer um pouco mais sobre o nosso trabalho de consultoria, entre em contato conosco que ajudaremos você a alcançar a eficiência que tanto deseja!