Desperdício gera custo e custo é o nosso inimigo. Portanto, devemos eliminá-los imediatamente!
O pensamento enxuto (lean linking) é uma filosofia japonesa nascida na Toyota em meados do século 20 que se tornou conhecido no ocidente por volta dos anos de 1990. Esta filosofia tem como uma de suas metas a de reduzir os desperdícios nos fluxos de valor.
No início do desenvolvimento do Sistema Toyota de Produção, foi criada uma lista dos 7 desperdícios que deveriam ser eliminados ou reduzidos. Ao estudar o STP e trazê-lo ao ocidente, percebeu-se a existência de um oitavo desperdício, o de capital intelectual humano.
A obrigação de todos os profissionais é aprender a enxergar estes desperdícios e eliminá-los ou reduzi-los assim que possível. Entretanto, para que isso seja possível, devemos conhecê-los antes.
Os 8 desperdícios do lean manufacturing
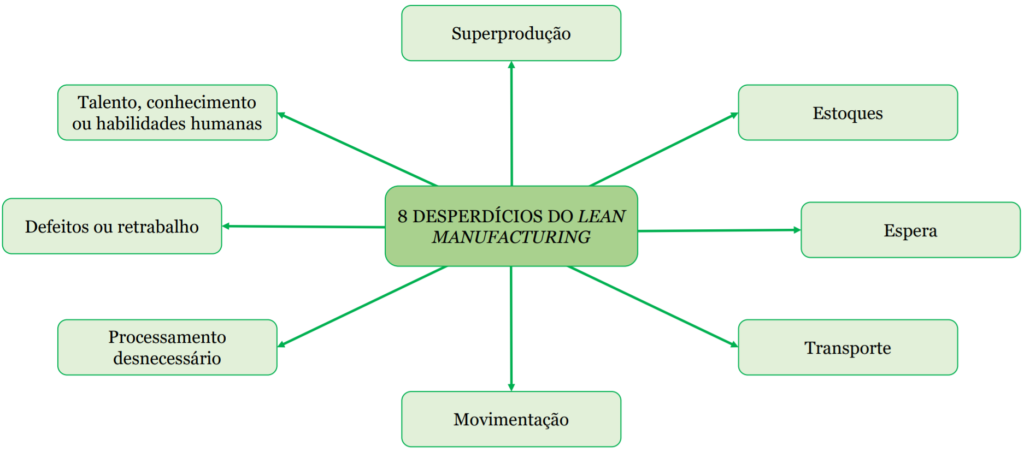
Superprodução
Quando produzimos antes ou em maior quantidade que o necessário, estamos gerando desperdício. Geralmente é causado pela ilusão dos gestores de que uma máquina ou processo deve produzir o máximo que pode individualmente, sem considerar as instabilidades que isso pode gerar caso os processos posteriores no fluxo estejam com uma velocidade menor.
A justificativa para a prática deste desperdício geralmente é a errada ideia de que, para otimizar a produtividade em um cenário de Setup demorado, precisamos aumentar o tamanho dos lotes de produção. Fazendo isso, estamos escondendo o problema real – o tempo alto de troca entre um produto e outro!
Este desperdício caracteriza a produção empurrada, e é considerado o PIOR dos 8 listados, pois ele gera ou aumenta todos os outros da lista. Ou seja, quando produzimos em excesso, aumentamos os estoques, defeitos, transporte, movimentação, etc.
Estoques
São materiais parados ao longo do processo produtivo. Vale lembrar que material parado é igual a dinheiro parado, e não queremos isso!
Os estoques são divididos basicamente em 3 tipos:
- Matéria Prima
- Estoque de processo – work in process (WIP)
- Produto acabado
Os estoques de matéria prima e produto acabado são estratégicos e dependem do objetivo e da saúde financeira de cada empresa. Eles devem dar segurança ao nosso processo de que não sofreremos com o aumento de preços ou a falta de matéria prima para produção e que nossos clientes não ficarão sem os nossos produtos.
Já o estoque de processo (WIP) é onde moram os desperdícios. Se um processo “A” produzir mais do que o processo posterior “B”, teremos entre os dois a formação de um estoque. Caso a máquina do processo B tenha um defeito e não consiga processar o material recebido, um estoque também se formará.
O principal problema do estoque é que ele gera custos para a empresa, devido principalmente ao custo de oportunidade do dinheiro investido em sua compra, o custo de armazenamento ou os custos da perda do produto por fim da validade ou avarias em transporte. Portanto, devemos identificar a causa ou a decisão estratégica que gerou cada ponto específico de estoque e reduzi-los ou eliminá-los por completo. Uma dica é mapearmos cada um dos fluxos de valor da organização (passo a passo aqui) para facilitar este entendimento e tomarmos a melhor decisão.
Espera
É o famoso desperdício de TEMPO, aquele que não volta mais!
Consideramos desperdício qualquer pessoa, máquina, processo ou planta que esteja parado esperando “algo” para realizar a atividade. Isso se deve geralmente à falta de material ou à ineficiência de uma máquina ou processo inferior.
Para evitarmos este desperdício, devemos balancear o nosso processo produtivo em função do tempo TAKT (ritmo definido pela demanda em função do tempo), construindo fluxo contínuo onde possível e produção puxada nos demais casos.
Transporte
É o desperdício caracterizado pela movimentação de materiais ou equipamentos no processo além do necessário.
Este deslocamento excessivo geralmente é causado por grandes distâncias entre os processos ou áreas, por má organização ou por estoque maior que necessário. O transporte geralmente é feito por carros kit, paleteiras, empilhadeiras ou caminhões e gera gastos com a compra destes veículos e com combustível, além de consumir tempo de trabalho operacional.
Para evitar este desperdício, devemos aplicar os conceitos do 5S e fluxo contínuo de produção.
Movimentação
É o excesso de deslocamento ou movimentações feitas por pessoas ou máquinas para buscar ferramentas, preencher formulários, levantar peças, dobrar, girar e qualquer outro movimento na realização da atividade como um todo.
O desperdício de movimento é o maior responsável pela fadiga operacional e, além de aumentar o custo do produto devido ao tempo gasto, gera desmotivação da equipe, problemas de ergonomia e riscos de segurança devido ao cansaço.
Para reduzir ou eliminar este desperdício, recomendamos a realização de kaizens de processo e a aplicação de 5S.
Processamento desnecessário
Corresponde ao excesso de etapas de processamento. Ou seja, um processo ou atividade inteira realizada sem necessidade! Este desperdício é comum quando não conhecemos realmente o nosso cliente e consequentemente não entendemos o que ele enxerga como valor em nosso produto. Devido a essa falta de conhecimento sobre o valor, fazemos atividades ou agregamos acessórios ao produto que o cliente não necessita e muitas vezes nem sabe que existe.
Este processamento, apesar de não agregar valor ao produto, gera custos e aumenta o lead-time total.
Recomenda-se a prática do mapeamento do fluxo de valor para que estes processos sejam identificados e, na medida do possível, eliminados. Também lembramos que os padrões de trabalho devem ser revisados constantemente, pois o padrão que é bom hoje, pode não servir amanhã.
Defeitos/Retrabalho
É o desperdício da falta de qualidade dos nossos processos. Quando produzimos com qualidade abaixo do especificado, precisamos gastar recursos para retrabalhar o produto ou mesmo descartá-lo por completo.
É importante lembrar que, na maioria dos casos, o problema de qualidade não é originado por um funcionário ruim, e sim por um processo ruim ou por falta de padrão de trabalho ou treinamentos. Devemos criar processos organizados, fáceis de entender através de gestão visual e com sistemas à prova de erros, onde qualquer problema de qualidade seja facilmente detectado e resolvido (no curto e no longo prazo).
Desperdício de talento/habilidade/criatividade
É a falta de envolvimento das equipes operacionais nas decisões do negócio. Também consideramos desperdício quando um dos nossos colaboradores que realiza a atividade de uma forma ágil e sem defeitos não padroniza o seu método. Ou ainda, quando um dos colaboradores se aposenta ou é demitido da empresa e leva consigo todo o conhecimento.
Devemos buscar sempre o envolvimento das equipes de trabalho nos kaizens, nas mudanças de layout, nas compras de máquinas, na resolução de problemas e demais atividades que requerem conhecimento sobre o processo. Afinal, eles estão lá no gemba durante 8 horas ou mais por dia, e conhecem melhor do que ninguém o que acontece na sua área de trabalho.
Como identificar os desperdícios na prática?
Para identificar os desperdícios na indústria, escritório, construção ou qualquer que seja o negócio, é recomendado uma atividade chamada “caminhada no gemba”. O conceito do “genchi gembutsu” significa ir até o local onde a atividade acontece (gemba) e observar como as atividades são realizadas, qual e como o valor é gerado, qual o fluxo de produção, quais os padrões de trabalho e, é claro, observar os 8 desperdícios.
Recomenda-se formar uma equipe de até 8 pessoas, de departamentos diferentes e, juntos, visitarem uma área específica durante 20 minutos, observando o processo acontecendo naturalmente. Todos devem ter papel e caneta suficientes para fazer rascunhos dos desperdícios observados.
Antes de se deslocar ao local, a equipe define um líder, que explicará ao líder da área e aos trabalhadores que esta é uma atividade para gerar oportunidades de melhoria e que a equipe estará lá para ajudar e não para julgar! O líder cronometra o tempo da visita, confere os EPIs em todos os participantes, garante o respeito entre os envolvidos e comunica o fim da atividade. Então, a equipe se dirige a um local de reunião, onde, de forma organizada e dando a todos a oportunidade de comentar, as oportunidades são levantadas e anotadas em ata pelo líder.
O próximo passo é reunir uma equipe e começar um kaizen neste processo para eliminar os desperdícios encontrados!
Caso ainda tenha dúvidas sobre os desperdícios ou queira conhecer um pouco mais sobre o nosso trabalho de consultoria, entre em contato conosco que ajudaremos você a alcançar a eficiência que tanto deseja!