O mundo gira, a demanda cresce, a máquina quebra, os colaboradores se aposentam, o custo aumenta!
Toda empresa ou profissional que visa o sucesso ao longo prazo deve melhorar a cada dia. Afinal, aquilo que eu faço de bom hoje, pode não ser bom amanhã. Portanto, precisamos cultivar uma filosofia de melhoria contínua.
O kaizen é a filosofia dentro do pensamento enxuto que nos ensina a melhorar continuamente.
O que é kaizen?
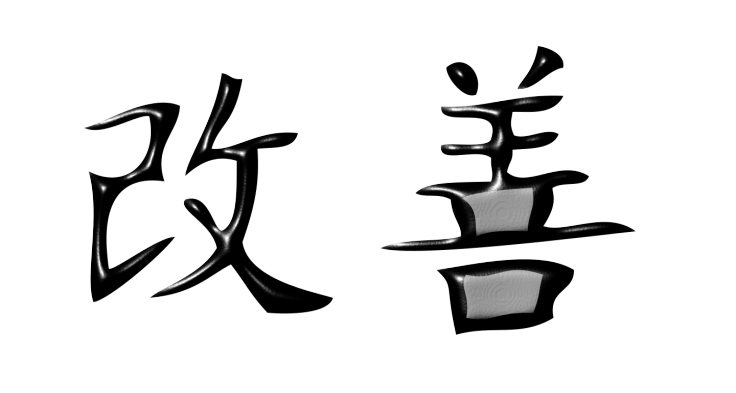
Kaizen é uma palavra japonesa que significa “mudar para melhor”. Em outras palavras, precisamos mudar a forma como fazemos as coisas para, depois disso, encontrar um resultado melhor.
A Toyota, desde sua origem, foi uma empresa que melhorou seus produtos e processos dia após dia, fazendo com que se tornasse um exemplo de excelência no ramo automotivo. Isso foi possível devido à cultura de melhoria contínua criada desde seus cargos mais altos até o chão de fábrica. Na prática, a direção e a gerência das plantas coordenam os conhecidos kaizens de fluxo, enquanto os líderes e suas equipes de trabalham aplicam os kaizens de processo.
Kaizens de fluxo: são melhorias realizadas em todo um fluxo produtivo, de porta à porta, passando por diversos processos e até a entrega de um valor. Geralmente estes trabalhos possuem longa duração. O mapa de fluxo de valor é uma ótima ferramenta para orientar este tipo de melhoria.
Kaizens de processo: são melhorias pontuais, realizadas pelas próprias equipes de trabalho, visando resultado em eficiência de um processo específico. Portanto, estes possuem curta duração e buscam principalmente eliminar os 8 desperdícios.
Para nossa alegria, ambos os tipos de kaizen são baseados no conceito PDCA, de Edward Deming.
O que é PDCA?
A “roda do PDCA” é um método simples de gerenciamento para projetos de melhoria contínua, o qual nos indica 4 passos principais:
- Plan (Planejar): Descreva e analise a causa raiz do problema, defina o objetivo, forme uma equipe e crie um plano para alcançá-lo.
- Do (Fazer): Execute as ações conforme planejado.
- Check (checar): Verifique o resultado das medidas tomadas em relação ao objetivo.
- Act (agir/ajustar/padronizar): Faça ajustes após verificar um resultado abaixo do esperado ou padronize o processo caso o objetivo tenha sido atingido.
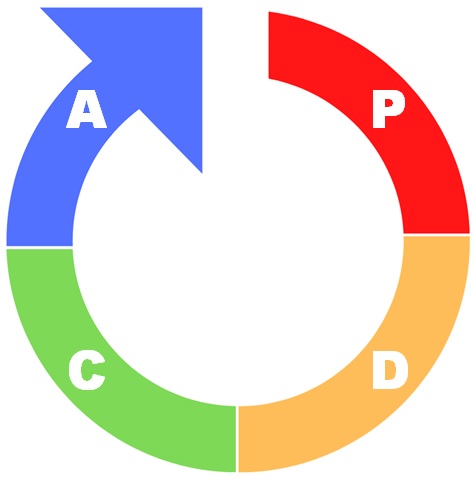
Esta roda de melhoria representa um ciclo, que se repete quantas vezes forem necessárias para que se obtenha os resultados desejados.
Como fazer um kaizen na prática?
Reúna papel, caneta e cronômetro pode ser o do celular, caso a empresa permita seu uso e vá até o gemba (local onde as coisas acontecem – chão de fábrica, canteiro da obra…) estudar o processo. Anote tudo que puder e siga o nosso passo a passo:
Planejamento
1. Descreva o problema
Conte uma história, coloque fotos, mapas ou o que for necessário para justificar o trabalho que está sendo feito. Acima de tudo, a descrição deve conter as informações necessárias sobre a realidade atual para direcionar o trabalho.
2. Forme uma equipe multifuncional
Convide pessoas com conhecimento e autonomia para fazer o trabalho fluir. Uma das pessoas deve ser nomeada como “líder do kaizen“, que ficará responsável por garantir que haja respeito entre os envolvidos, cumprimento do plano de ação, etc.
3. Analise a causa raiz do problema com a equipe
Utilize ferramentas como Brainstorming (tempestade de ideias), Diagrama de espinha de peixe (ishikawa), 5 porquês ou qualquer outra ferramenta que transforme o seu PROBLEMÃO em probleminha. Em outras palavras, transformaremos em um problema simples e barato de resolver e que gere grandes resultados.
4. Defina o objetivo e a data fim
Coloque metas em resposta ao problema e defina prazos atingíveis. Estes prazos devem estar de acordo com o que a empresa precisa e que a equipe tem condições de atender.
5. Confeccione o primeiro plano de ação
Defina as ações pontuais, com responsável e datas de início e fim. Não deixe nada de fora.
Execução
6. Cumpra as ações planejadas
Realize as ações dentro do prazo estipulado e da maneira ideal para alcançar o objetivo. Se necessário, apresente todo o projeto à quem realizará as ações ou faça treinamentos.
Checagem
7. Acompanhe os resultados das ações tomadas
Realize este passo através de reunião com a equipe, conversas com os trabalhadores do processo, acompanhamento de indicadores, etc. Entenda se o resultado obtido com as ações foram suficientes para alcançar o objetivo ou se precisa realizar novas ações.
Ajustes ou padronização
8. Padronize o que deu certo
Crie padrões visuais, comunique todos os envolvidos, realize treinamentos e crie procedimentos operacionais padrão (POPs) caso necessário. Neste passo, precisamos garantir que aquilo que funcionou será feito por todos e em todas as horas.
9. Ajuste o que deu errado, reiniciando o ciclo PDCA
Se o objetivo ainda não foi alcançado, a equipe deve rever o plano, criar novas ações e executá-las quantas vezes forem necessário para alcançar o objetivo.
Dicas práticas para um bom kaizen:
- Esteja sempre aberto a mudanças;
- Analise todas as ideias e dê oportunidade para que toda a equipe tenha voz;
- Evite ações de alto custo
- Não procure culpados
- Não invente desculpas
Para finalizar, nós da Geração Lean compilamos os passos deste tutorial na imagem abaixo.
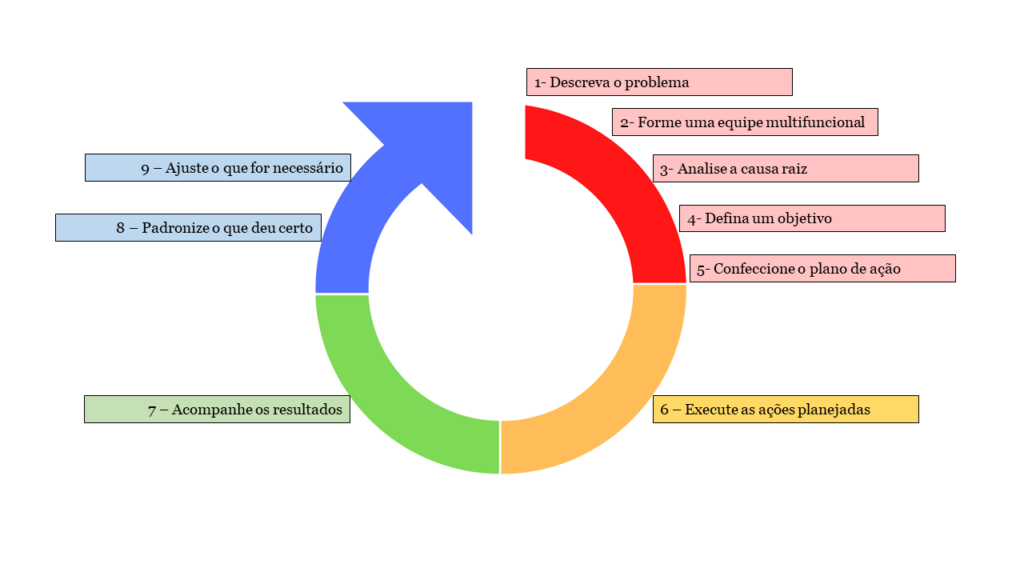
É importante lembrar que, conforme citam Liker e Convis em Modelo Toyota de Liderança Lean (2013), “Kaizen não é a atividade de melhoria, ou a semana da atividade, mas sim o conceito com o objetivo de melhorar diariamente”. Portanto, devemos aplicar este conceito como cultura, melhorando a cada dia e dando o nosso melhor em tudo o que fazemos.
Para mais orientações sobre kaizen ou demais ferramentas lean, entre em contato conosco por aqui.